Revolutionizing the Manufacturing Industry with Advanced Technology
“Boosting Production Efficiency and Product Quality Through Digital Innovation”
At HMD Technical Services, we specialize in enabling manufacturing companies to adopt cutting-edge technology that transforms their production processes. The manufacturing industry, while foundational to global commerce, faces constant challenges related to operational efficiency, cost reduction, and product quality. This case study highlights how we partnered with a leading manufacturing company to address key challenges in their production line, supply chain management, and quality assurance. By deploying advanced automation, AI, and cloud-based solutions, we helped them achieve remarkable improvements in operational efficiency and overall business performance.
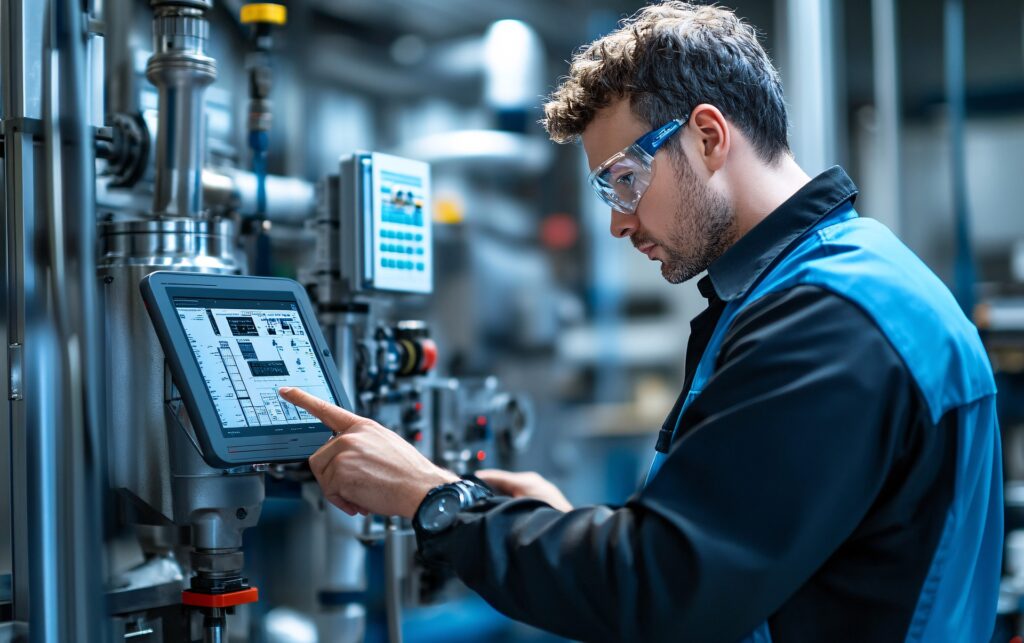
Challenges
Despite its long-standing reputation, the manufacturing company encountered several significant obstacles:
- Inefficient Manual Production: Many production tasks were still carried out manually, slowing down output and introducing potential for human error.
- Quality Control Issues: The manual nature of inspections and quality control checks often led to delays and inconsistencies in product quality.
- Supply Chain Delays: Managing the supply chain was a cumbersome process, often resulting in material shortages or delays in fulfilling orders.
- Limited Data Integration: Different departments, including production, quality control, and logistics, worked in silos with limited data sharing, leading to missed opportunities for process optimization.
Solutions Provided
To address these issues, HMD Technical Services implemented a suite of innovative solutions tailored specifically for the manufacturing sector:
Robotic Process Automation (RPA)
We introduced RPA to automate key manufacturing and operational processes, including:- Automated Assembly Line Tasks: RPA was deployed to automate repetitive tasks such as assembly, packaging, and product labeling, increasing efficiency while reducing the risk of human errors.
- Automated Quality Inspections: Robots equipped with machine vision were used to perform real-time quality inspections on the production line, identifying defects instantly and ensuring consistent product quality.
Artificial Intelligence (AI)
Our AI-powered tools helped improve production performance and predictive maintenance, including:- Predictive Maintenance: AI algorithms were implemented to monitor equipment and predict potential failures, allowing for proactive maintenance and reducing downtime.
- Quality Control Optimization: AI was used to analyze production data in real time, providing insights that helped to fine-tune processes and reduce defects.
Cloud-Based Solutions
We migrated the company’s data and operational processes to a secure cloud platform, providing:- Real-Time Access to Production Data: Plant managers and executives could access production metrics in real time, enabling better decision-making and quicker responses to any issues.
- Enhanced Collaboration: Cloud-based systems allowed different departments to collaborate more effectively, improving communication and ensuring smooth operations across the entire production lifecycle.
Supply Chain Automation
To streamline the supply chain, we introduced automation solutions to manage procurement and inventory more effectively:- Automated Procurement: Implemented systems that automatically ordered raw materials based on production needs, reducing the risk of stock shortages and minimizing delays.
- Inventory Management: Automated inventory tracking provided real-time visibility into stock levels, enabling better demand forecasting and reducing the chances of overstocking or understocking.
Implementation Timeline
Phase 1: Assessment and Strategy (Month 1)
Conducted a thorough analysis of the company’s production processes and supply chain management, identifying areas for automation and AI integration.Phase 2: Technology Deployment (Months 2-4)
Rolled out RPA solutions on the production line, integrated AI-powered predictive maintenance systems, and initiated the migration of data to the cloud.Phase 3: Supply Chain Automation (Months 5-6)
Automated procurement and inventory systems were implemented, streamlining supply chain operations and improving overall production efficiency.Phase 4: Monitoring and Optimization (Month 7)
Monitored the performance of all newly implemented solutions, gathering feedback from production teams and continually optimizing systems for peak performance.